Soft start is a step-down start, which means that the motor starts slowly at a lower current, so that the impact on the power grid is small, and at the same time it can reduce the load margin of the transformer and the control circuit, and at the same time improve the service life of the equipment. Generally, when the AC motor is started directly, the starting current is 6~10 times of the test running current, but after using the soft start technology, the starting current is reduced to 1~3 times. The instantaneous current of a hard start of a high-power motor is particularly large, and the impact on the power grid is very large, so the starting voltage is reduced to reduce the impact on the power grid. The usual soft start method is a star-delta step-down start. The principle is that when the motor winding is star-connected At this time, each group of coils will withstand 1/1.732 times the voltage of the transmission voltage (that is, the reciprocal of the square root of 3). When the motor windings are connected in delta, each group of coils will directly withstand the transmission voltage, thus realizing soft start. The disadvantage of soft starting is that the starting torque is small.
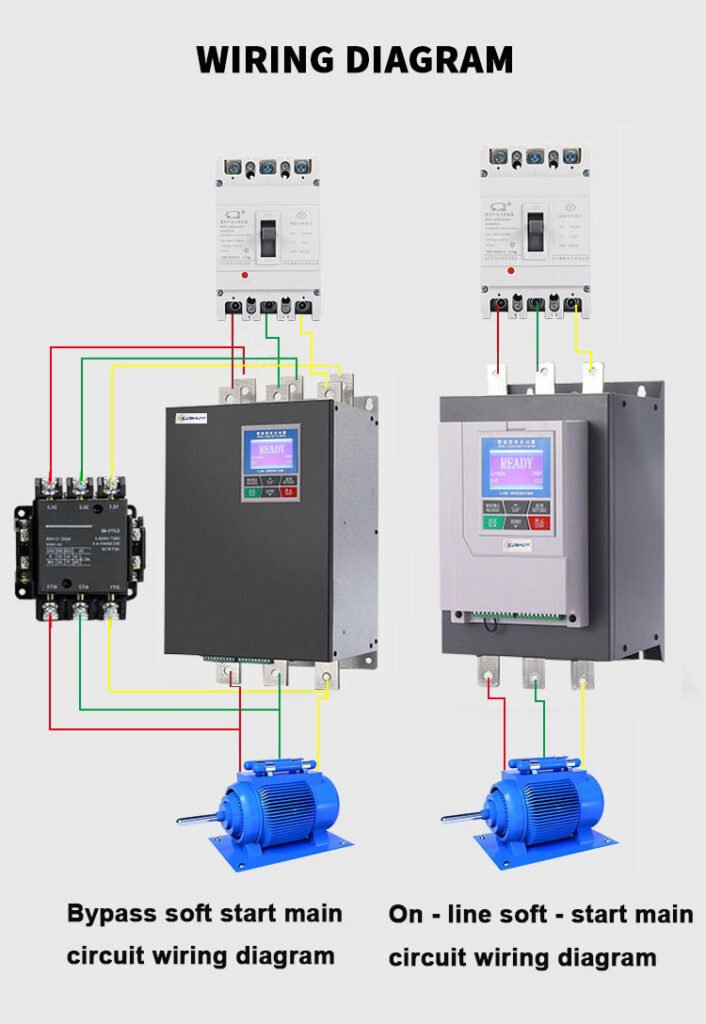
The soft start of the motor mainly adopts the following methods:
- Reduce power supply voltage to start
- Reduce power frequency to start
- Reduce the excitation current to start a hard start (direct start) The starting current is 3-7 times the rated current of the motor. When starting directly (hard start), this situation of exceeding the rated current of the motor has brought many problems that are restricted to the manufacturing process and structure of the motor itself. The disadvantage of hard start is that the instantaneous current is particularly large and has a large impact on the power grid.